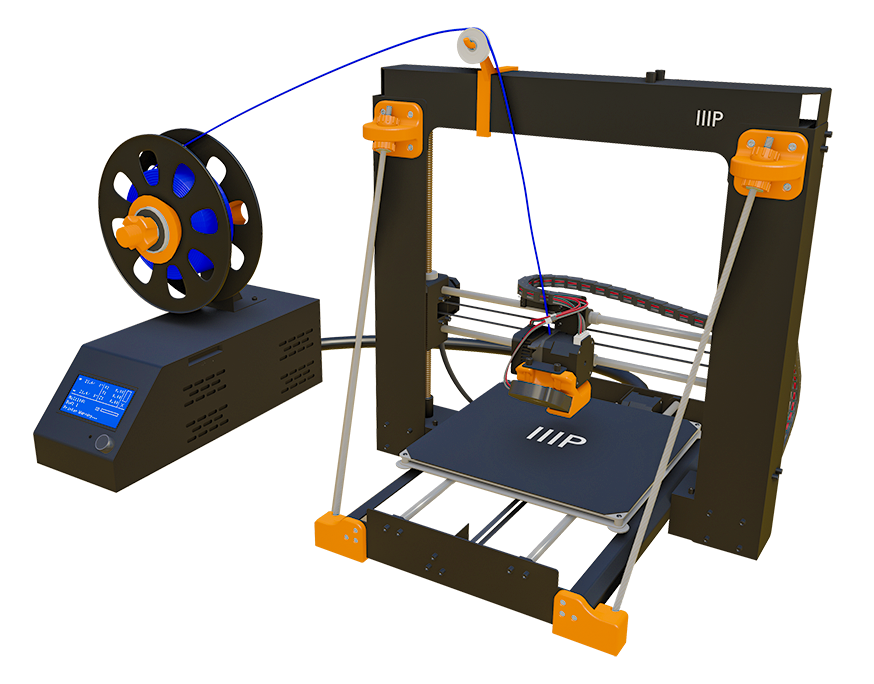
Intro
While the Maker Select V2 is a good printer, out of the box it could use some help in the quality department, this is were some handy modifications can help the printer improve the final products. In the episode, we will focus on the overall stability of the printer, as even minor vibrations can affect the final outcome. Let’s get started!
Full Overview
Watch the overview video or keep reading the full article below
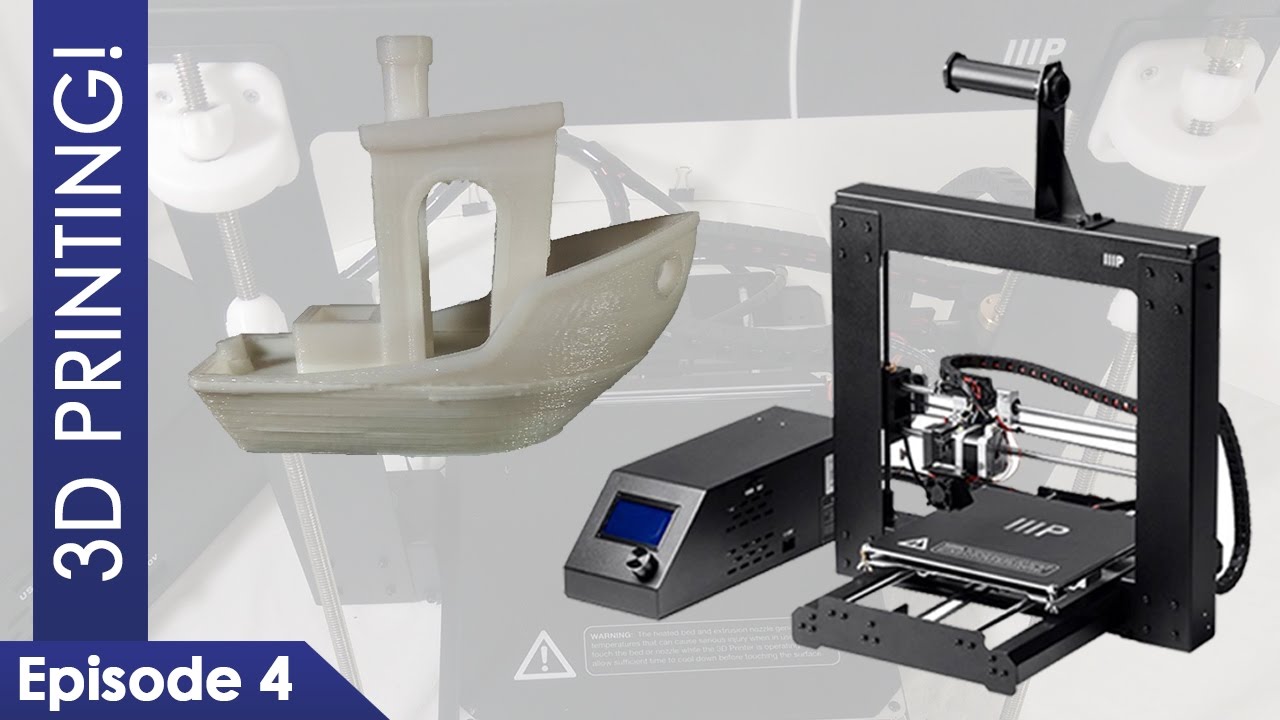
Table of Contents
Mods and the Benchy
The last episode we printed a replica Cherry MX keycap and just touched the surface of support structures. There were a couple takeaways from that episode that have been incorporated in this episode, thanks to all my subscribers for the suggestions!
While the maker select v2 is a good printer, it can be even better with a few modifications. In this episode, we are going to investigate one of the most important of these modifications, the Z-axis gantry brace.
But before we make any modifications to the printer we need to set a benchmark so that we can see if our modifications are making a difference. Of course one of the best and most popular benchmark prints is the 3D Benchy.
More on the Benchy
The 3D Benchy is designed to push any 3d printer to its limits with a wide array of challenging geometry that will reveal even subtle issues related to the 3D printing process. Examining the results of the Benchy can help determine where to focus modification efforts to get a better result next time.
Anyone can download the files for the 3D Benchy by visiting its official website at 3dbenchy.com and going to the download section where you can select from a number of repositories for the files. I used Thingiverse since they are already an amazing source of all things 3D CAD, a link to it will be in the description below. Simply download the zip file, extract the files, open the “Files” folder within and select the 3DBenchy STL model. In your favorite slicing program confirm all your settings. I went with normal quality, 20% infill, and no support structure. Save it to Gcode and start printing.
With these settings, it should take about 2 hours.
2 hours later, it’s done.
Benchmark Results
The most obvious thing you notice is this hard line in the lower third of the boat. This was caused by a change in the filament. I think it’s absolutely amazing the difference in quality between the two layers, I didn’t expect much if any change at all. The bottom third was using some generic PLA that came with the printer while the rest of it is using Worksteel “high precision” PLA, who claim to have 0.02mm dimensional accuracy and with the Benchy it shows, at least compared to the generic PLA. Link to the Worksteel filament will be in the description.
You see various artifacts and overall poor quality with old PLA but once the Worksteel filament started flowing the quality shot up. The lip of the deck is clean and sharp, there is no stringing in the gaps of “cockpit”. The only thing that really stands out can be seen at the top of the doorway and windows where the bridge or arcs were a little trickier for the printer to make sharp.
Honestly, I was amazed it was able to bridge the gap for the front window at all. I obviously have to have more faith in this printer. Compared to other Benchy’s I’ve seen from unmodified printers in this price range I’m extremely happy! I’m not an expert at interpreting the results so if you peeps see something of concern that I didn’t mention please don’t hesitate to leave a comment below!
Seeing the difference in the quality of filament makes me want to go back and print my other models again to see how different they may turn out. I might just do that later.
The Brace Mod
So now we have our benchmark and while I don’t see the major issues that I’ve seen in other Benchy’s there was still something I noticed while watching this and previous prints, and that is the obvious wobble of the vertical gantry especially when the bed and extruder moved in quick succession. The wobble was amplified when I put on the new spool of filament since there was more weight on top. This wobble will adversely affect any print but especially ones that are tall.
This is where our first and probably most important mod will come into play. The Z-axis gantry brace does pretty much what it sounds like. It will support the top gantry and keep it from moving around during printing. This is done by essentially attaching a support structure from the top of the gantry arm diagonally to the front of the base.
The really cool thing is anyone can do this. It uses a few printed pieces and some hardware you can find at any local home improvement store like Home Depot, Lowes, or Ace Hardware.
There are a handful of different pieces that we will need to print but they can all be found in one zip file on Thingiverse at the link in the description. While there are a few different configurations available they all accomplish the same goal. I’ll take you through the one I chose which does require a few more pieces than the other configurations but I believe offer better fine-tuning in the final product.
Once you’ve downloaded the zip file and extracted everything inside you’ll find a not small group of STL files. We are going to focus on the following 7 models.
TopLeft, TopRight, BottomLeftForBalls, BottomRightForBalls, BackFootLeft, BackFootRight, BallsMk2
Most of these are mirror sets of each other.
A quick overview of the pieces, TopLeft and TopRight will be attached to the top of the gantry frame and will hold the rods in place at a slight inward angle, with the help of some bolts and pairs of BallMk2 fasteners for each. We will simply call them the top mounts
BottomLeftForBalls and BottomRightForBalls will have the other end of the rod attached to the base. Each one of these will use just one BallMk2. These two pieces have large areas on the bottom that will actually go under the base of the printer, we will use this area to attach shock absorbing feet to further isolate the vibration coming from the printer. We will simply call them the bottom front mounts.
The BackFootLeft and BackFootRight to not directly contribute to the brace but they also have a large areas on the bottom that will go beneath the base to attach more shock absorbing feet. We will simply call them the back mounts
Lastly the BallsMk2 is basically the bolt fasteners that will help tighten down and hold the bolts in place, I choice the Mk2 version because it has ridges on the outside to make adjusting them by hand easier. We will simply call these bolt fasteners and will require 6 of them.
As the creator put it, these pieces are “over engineered” which is a good thing because you want them to last but be wary that it is going to take some time to print all the pieces, roughly 16 hours and use 44 meters or 144 feet of filament at normal quality with a 20% infill so be patient. You can print all the piece in one go but I thought it better to go one at a time, all though I did printer 3 bolt fasteners at a time.
Getting This Mod Installed
After you are done printing all these pieces there is very little in the way of cleaning them up. One thing you’ll have to do is remove the interior support pillar of bolt fasteners by simply bending it with a small screw driver or pliers, it snaps right off. The only other thing I did was lightly file the screw holes on the bottom brackets with my precision round needle file.
Now for the actually hardware you’ll need for the configuration we are going with: 2 x 410mm or 16 inch lengths of 8mm or 5/16 inch threaded rods, Ace Hardware like other home improvement stores sell these robs in 3 foot or 910mm pieces so you only have to buy one and cut it to length. I used a powered angle grinder to make quick work of the cuts. You can use a hack saw but for a clean edge I’d recommend the angle grinder or ask someone at the home improvement store cut it for you, they usual will for free or for a nominal fee.
Next up are 20 x M3 by 10mm screws, these can be longer but make sure you have the clearance before you buy longer ones. Than 6 8mm or 5/16 inch nuts
Lastly 2 8mm or 5/16 inch locking nuts
There is a pre-made hardware kit on the ultimate 3d printing store .com website that runs for $21 and includes the bolts, screws, and threaded rods cut to length, link to that below. While this is a great option I went ahead and picked up my stuff at Ace Hardware which turned out to be ever so slightly cheaper plus I picked up a squaring tool and few other things for later mods.
Now we have everything we need to put it all together. Start by attaching the bottom front mounts, simply take out the original screws, lift up the printer slightly, align the mount, use 3 M3 screws to fasten it in place, don’t tighten it down all the way just yet.
Attach the back mounts in a similar manner
Next, the top mounts, first make sure you are putting the correct piece on the correct side because each one is slightly different and you won’t realize it until you try and insert the rods. Pro tip here, instead of removing all 4 screws from the corner at once, take only one out, attach the mount, and then remove and replace the other three. This will save you from having to realign the gantry frame.
With all the mounts in place go ahead and tighten the screws down. On each rod slide a nut on both ends going about a quarter of the way in and then slide on two of the bolt fasteners. Now to install the rods, slide them up through the bottom of the top mount. With them in a vertical position slide on another bolt fastener and bolt, doing this pieces now will save some headache later. Now carefully lift up the rod and let it settle into the bottom mount.
Attach the locking nuts from underneath the bottom front mounts. I found it easiest to slide the rod through the mount about an half an inch, screw on the nut until it locks and slide both back into the mount.
This is where the squaring tool comes in. You want to make sure the printer stays as square as possible as you tighten the bolt fasteners. Start by tightening down the bottom fasteners until they are snug.
The fasteners of the top mounts are going to be used to fine tune the brace; adjust these until the printer is perfectly square on both sides. If the frame is leaning toward you adjust the bottom fasteners up, if it’s leaning away from you adjust the top fasteners down. Double check everything is tightened down and square once again, make adjustments as needed.
Lastly attach a rubber and/or felt pad to the bottom of each mount under the base, any kind will do here so it’s up to you but I wouldn’t spend a whole lot of money on them.
And that’s it! We are done. You can clearly see how stable it is with the brace compared to without it. I really think this is one of the most important mods you can make to printers of this type and I highly recommend you do it if you haven’t already.
There are few thing you can do to make it look better like adding binder clips to the rods to classy them up a little but I personally like the industrial look, I mean it is a 3D printer. I’m more interested in how the models look compared to what made it.
Benchmark the Benchmark and Conclusion
So what to do now? Let’s check our benchmark! This time I won’t switch up the filaments in the middle of the print.
The results, of course, it’s much cleaner than the last one but that more because it’s come from one roll of filament. Like before the arcs and bridge on the top have the same issue. I did notice however the surface of the roof is just a bit smoother than before and the definition of the lip of the deck is ever so slightly sharper. I think it’s beautiful. Again I’m no expert so if you see something I didn’t mention please leave a comment.
This is has been an exciting project and I’m very happy with the results. Of course, there are quite a few more mods that will continue to improve the print quality, I will continue to investigate the more applicable ones and bring them back to you soon.
Special thanks again to my subscribers that recommended the Benchy print and the z-brace mod, you’re awesome!
The Conclusion
Well, that is it for episode 2, I’m really excited to keep exploring the world of 3d printing and to bring all of you along with me. I’ll be doing some more testing over the next couple weeks. Next time I’ll work on some practical models that I can use around the house or at work.